How Hydraulic Oil Seals Enhance Lift System Reliability
Hydraulic oil seal ensures leak-free performance, protects components, and enhances the reliability of lift and fluid power systems in tough conditions.
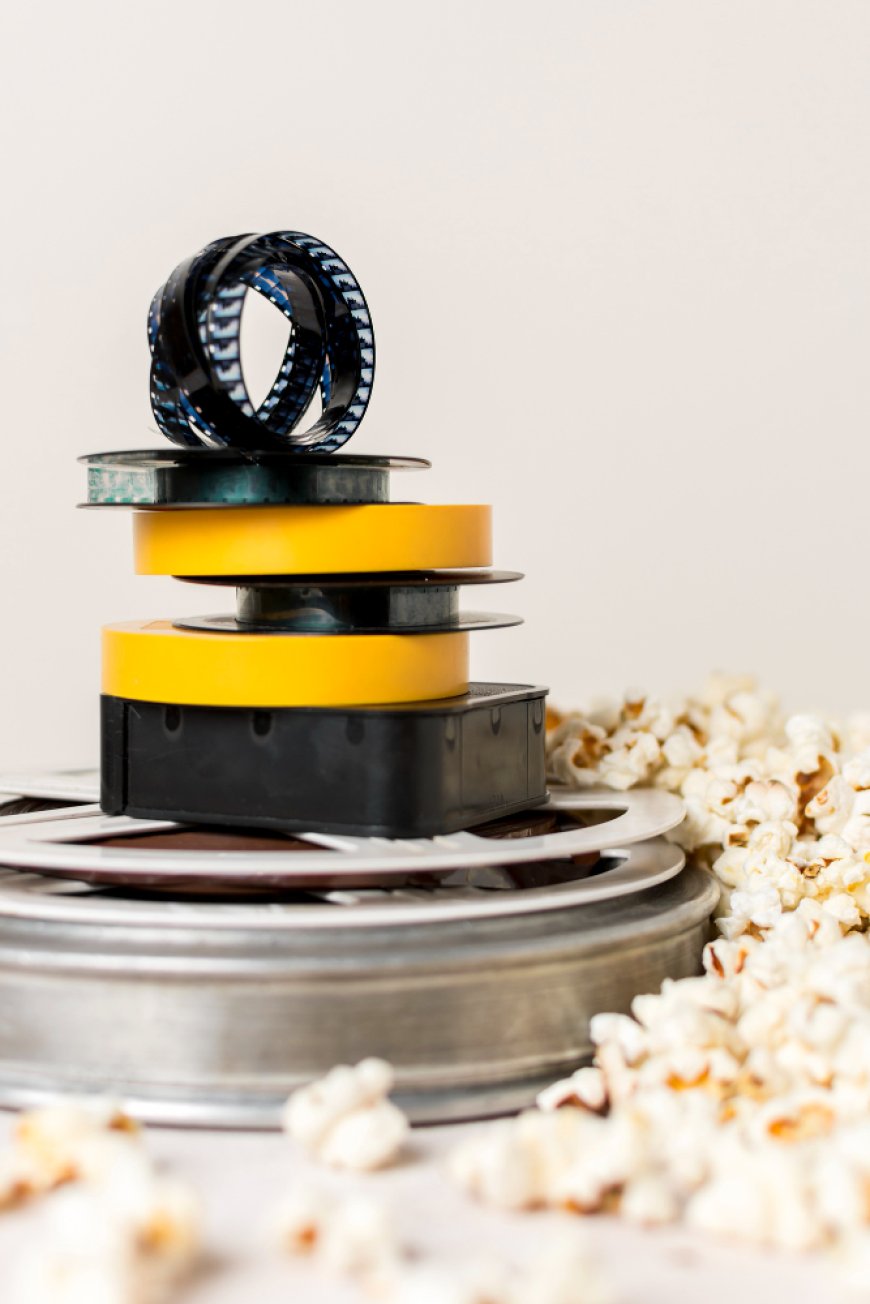
Introduction
In industrial and automotive settings, hydraulic lifts play an indispensable role in material handling, equipment maintenance, and vertical transport. Their performance depends on a seamless interaction between pressure control, mechanical components, and fluid dynamics. At the core of this system lies a small yet vital component—the hydraulic oil seal. Though often overlooked, this component directly affects the reliability, safety, and longevity of lift systems.
This article explores how hydraulic oil seal contribute to the dependable operation of lifts, reduce downtime, and prevent costly equipment failures in demanding work environments.
Understanding the Role of Hydraulic Oil Seals in Lift Systems
Hydraulic lifts operate by transferring force through pressurized hydraulic fluid. This pressurization depends on the integrity of the system's sealing elements. A hydraulic oil seal, typically placed around moving shafts and pistons, keeps hydraulic fluid contained within cylinders while preventing contaminants such as dust, water, or debris from entering.
When functioning correctly, these seals:
-
Maintain pressure within the hydraulic circuit
-
Minimize internal and external leakage
-
Extend the service life of pumps and cylinders
-
Ensure smooth, uninterrupted lift motion
In essence, a reliable oil seal upholds the entire system’s performance and safety profile.
Why Seal Integrity Is Critical for Reliability
Even a minor leak in a hydraulic system can lead to pressure loss, jerky movements, or complete system failure. When lift systems are used for critical operations—such as elevating heavy vehicles, supporting industrial loads, or handling sensitive goods—this kind of failure can have serious consequences.
Poor sealing leads to:
-
Reduced efficiency: Fluid loss decreases force generation, increasing energy consumption.
-
Overheating: Low oil levels can cause excessive friction and heat buildup.
-
Component wear: Contaminants can damage internal surfaces of cylinders, pumps, and valves.
-
Increased maintenance: Frequent repairs and oil top-ups add to downtime and operational costs.
A durable and properly fitted hydraulic oil seal prevents these issues and enables lift systems to operate under optimal conditions for extended periods.
Types of Hydraulic Oil Seals and Their Applications
Different lift systems demand different types of seals, depending on pressure levels, stroke cycles, and environmental exposure. Some of the most common include:
-
Rod Seals: Placed in the housing, they prevent fluid from escaping around the piston rod.
-
Piston Seals: Maintain separation between chambers to ensure bi-directional movement.
-
Wiper Seals: Clean debris off the rod before it re-enters the cylinder.
-
Rotary Seals: Used in rotating shafts or swivel connections found in articulated lifts.
The correct material composition—such as Nitrile (NBR), Viton (FKM), or PTFE—further ensures chemical resistance, temperature tolerance, and pressure durability. Choosing the wrong seal can result in rapid deterioration, regardless of equipment quality.
Key Benefits of High-Quality Hydraulic Oil Seals in Lifts
-
Leak-Free Operation
Effective sealing prevents oil from escaping under high pressure. This is essential for applications where even minor leaks could cause mechanical instability or environmental hazards.
-
Lower Maintenance Costs
Seals that resist abrasion, chemicals, and pressure fluctuations reduce wear and tear on system components. This lowers service intervals and repair expenses.
-
Extended Equipment Life
Clean, sealed systems reduce internal corrosion and protect sensitive parts. As a result, hydraulic lifts enjoy a longer service lifespan.
-
Improved Safety
A lift operating at consistent pressure offers predictable movement and load handling. This is especially important in high-traffic or high-risk areas where equipment failure could endanger workers.
The Link Between Sealing and Operational Safety
In industrial environments, safety protocols extend beyond just operator behavior. Equipment design and maintenance directly impact workplace safety outcomes. For instance, a failed hydraulic seal in a vehicle lift or cargo handler could cause sudden drops or pressure spikes—posing a serious hazard to technicians or bystanders.
That’s why reliable sealing solutions complement broader safety infrastructure—much like the Safety Features of Modern Industrial Sectional Doors, which protect personnel and assets through advanced mechanical safeguards. In both cases, mechanical integrity equals operational safety.
Best Practices for Seal Performance and Maintenance
To ensure consistent lift reliability, operators and maintenance teams should implement the following practices:
-
Regular inspections: Check seals for signs of wear, swelling, or cracking.
-
Proper lubrication: Use compatible fluids that won’t degrade seal material.
-
Clean environment: Minimize exposure to abrasive dust, moisture, and chemicals.
-
Correct installation: Improper seal fitment can cause premature failure.
-
Scheduled replacement: Replace seals based on cycle counts, not just visible damage.
Additionally, investing in training for technicians ensures that seal handling and fitting are done according to manufacturer guidelines.
Conclusion
Hydraulic oil seals may appear small in size, but their contribution to lift system reliability is anything but minor. By maintaining pressure, preventing leaks, and protecting against contamination, these seals play a foundational role in ensuring consistent, safe, and efficient lift operations across industries.
As industrial environments continue to demand higher performance with fewer disruptions, investing in the right hydraulic oil seal solutions—and adhering to strict maintenance practices—has become essential. In a world where downtime equals lost revenue, sealing integrity offers more than reliability—it offers peace of mind.